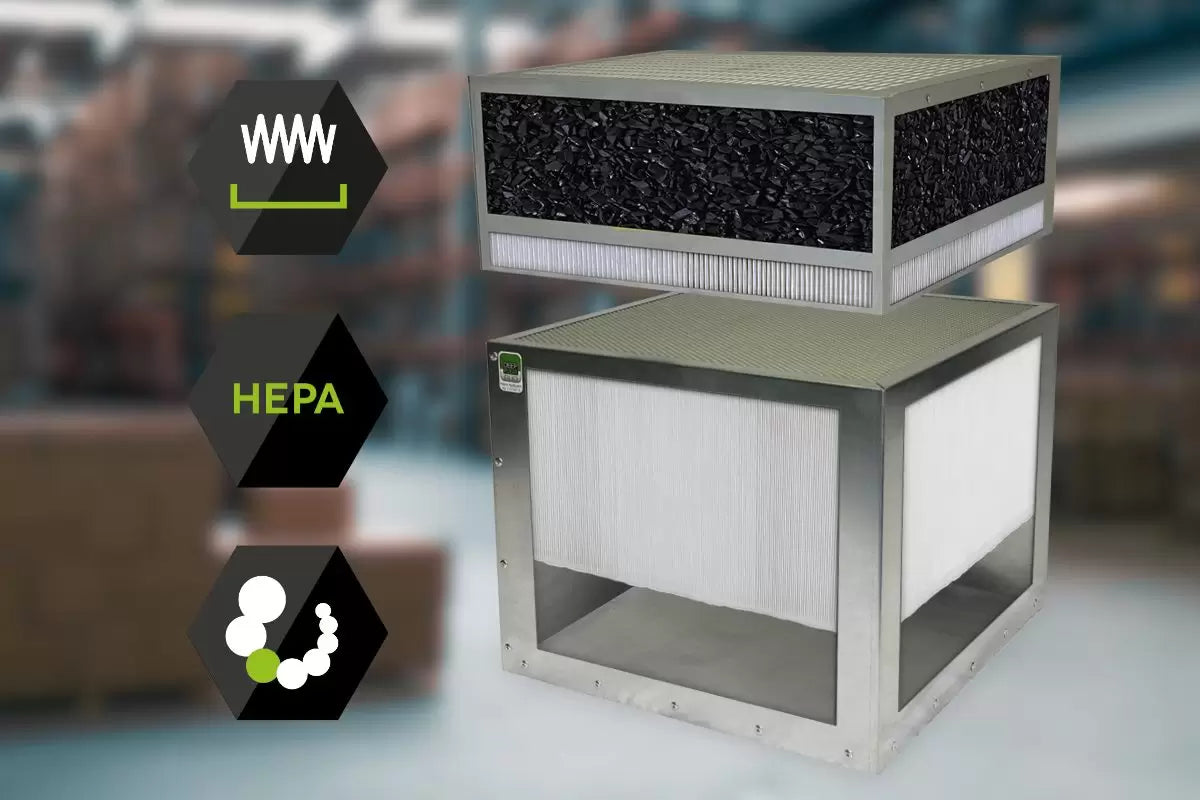
Three Steps to BOFA Filtration Efficiency
BOFA fume and dust extraction technology is used by businesses all over the world on a daily basis to increase productivity and control workplace safety.
Potentially hazardous airborne particles are filtered by BOFA's portable systems, which are used in additive manufacturing, lasering, electronics production, printing, and other processes that create dust and fumes.
The 3-stage filtration architecture used in most BOFA systems, when combined with sophisticated air flow management, offers excellent extraction performance, maximizes filter life, and contributes to a reduced total cost of ownership.
As Josh Evans, Applications Engineer at BOFA explains:
“BOFA filtration technology helps to reduce exposure to unwanted substances in the workplace. At the same time, our systems help keep production equipment free from dust that might otherwise impact on product quality. And because our technology is portable, it can support an agile manufacturing environment.”
The 1-2-3- of BOFA Filtration Technology:
Stage 1: The pre-filter such as our patented DeepPleat DUO, which incorporates a large capacity drop-out chamber to collect high volume of larger particulate. This helps capture the bulk of emissions, thereby optimising the life of the HEPA (High Efficiency Particulate Air) filter.
Stage 2: The HEPA filter is purpose-designed to create a large surface area capable of capturing 99.995% of particles at 0.3 microns, helping to protect operatives from airborne contaminants with potential to be harmful to human health.
Stage 3: A layer of activated carbon removes vapours and gases such as VOCs (volatile organic compounds), specially formulated to handle specific chemical interactions. The exact configuration, airflow rates and filtration media will depend upon each application and the industrial process involved.
If we compare processes such as manufacture of electronics and that of laser production, for example. For both processes, the HEPA and carbon filters will be identical, however due to large amounts of fume generated by laser processing, the pre-filter will need more capacity, whereas pre-filtration for electronics manufacturing will not require as much capacity due to lower volumes of fume being generated.
In the print industry, some wide-format printers use methyl ethyl ketone (MEK), sometimes known as butanone, as a solvent for printing. MEK reacts exothermically with untreated carbon. So, in this case, carbon that has been carefully processed and treated would be required.
Activated carbon filters are not required in mechanical engineering processes such as drilling and sanding as no gases or fumes are released during these activities. For this reason, extractors like the DustPRO line from BOFA are designed as a two-stage system that includes a pre-filter and a HEPA filter.
Find the perfect filter for your BOFA system from LEVFilterShop.com here, and improve your process efficiency with these three steps.
Have questions about BOFA filters or would like to know more? Chat to us using our LiveChat service, email us at info@levfitlershop.com or call us on 0141 892 6698.